The right materials can make or break the function of a custom coil cord.
A coil cord manufacturer does more to create a custom coil cord than just curl a straight cord into a spiral. Because they are meant to extend and retract, materials must be somewhat flexible in addition to the technical requirements dictated by the application. With the number of materials available, it’s difficult to choose the right one. Working with a cable assembly manufacturer can help you take the guesswork out of selecting materials that meet the needs of your project.
Conductors Used by a Coil Cord Manufacturer
At its simplest, a custom coil cord has the same basic structure as a standard straight cord: a conductor and some form of insulation and jacketing. The conductors are mostly metals like copper, tinned copper, and – in very special cases – alloys or composites can be used. However, unless you’re launching a satellite, running cable for the power grid, or implanting a gizmo into a human body, basic copper is what will be used.
Copper conductors (or stranding) start life as a rock. Then with the help of a lot of energy, they end up as a rod about the size of a Sharpie®, which is way too big for a coil cord. The majority of copper falls into two groups: those that contain oxygen and those that don’t. Copper with oxygen has improved abrasion and corrosion resistance so it is mostly used in power distribution and transmission. Copper without oxygen is more resistant to embrittlement which can occur when the Sharpie® is reduced to the size of a human hair. So oxygen-free copper is used extensively in cables that need to flex. Coil cords flex a lot, so most conductors or stranding used in them are made from oxygen-free copper. Copper with oxygen can be used to make coil cords, but, even though it’s lower in cost, Meridian will never use it because it fails much more quickly.
Once the copper stranding is the right size, the next step is to decide if it should be plated or not. Below are some choices for plating.
Bare Copper Conductors 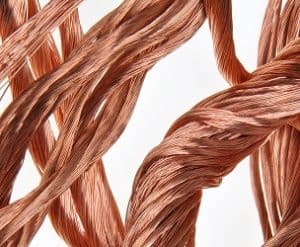
Copper without any type of plating is an inexpensive conductor material that can be a good choice if time and cost are considerations. However, this type of conductor is susceptible to corrosion and oxidation, which can hinder the connectivity. Since it is not as likely to corrode or oxidize, plated bare copper is more flexible. However, this type of copper is also harder to process after being made into a wire. Since it is bare, and oxygen is almost everywhere on Earth, this type of conductor oxidizes. An oxide layer on copper greatly reduces its conductivity and ability to bond with solder. So while bare copper can be used, and is more flexible, its service life is much shorter. If cost overrides quality/longevity in your application, then bare copper is an option, but the part will have a much shorter life, and that “life” starts the moment it leaves the wire drawing facility.
Plated/Coated Copper Conductors
Coating a copper conductor with a thin layer of “stuff” can offer additional benefits. However, it is also more expensive since it adds an extra step and more material is used. The most common coating on copper stranding is tin. This means the vast majority of copper conductors used in the electronics/telecommunications industry are tinned. Adding tin on top of the copper increases stiffness slightly but vastly improves its resistance to oxidation and corrosion. This improves the life of the resulting conductor greatly and makes processing much easier. The additional protection is especially useful in cables that are used near saltwater or are immediately exposed to air and not covered by some material.
Copper can be coated with other metals besides tin. For serious applications these coatings can be either silver or gold among others. Obviously these can add significant cost, but for some applications they are mandatory. Many medical, aerospace and military applications must have stranding with these types of plating since failure is not an option and extremely long life is required.
Aluminum Alloy Conductors
Aluminum alloys only have about 61% of the conductivity of copper, but they are less expensive and significantly lighter. In general, aluminum has greater endurance fatigue (ability to be bent back and forth without breaking) than copper. So based on its great fatigue resistance, one would think it would be a great choice for a coil cord. However, as noted, aluminum is much less conductive than copper. This is okay if you’re pumping kilowatts of power across a grid, but in most applications, this decrease in conductivity means too much loss of signal or power to make it a good choice for most coil cords.
Coil Cord Jacketing Material
Cable jacketing in a coil cord has two key roles: protection and memory. The jacketing protects the conductors from moisture, flame, chemicals, and other environmental factors. It’s also what gives a coil cord memory and makes it act like a spring. Copper is a “lazy” metal, meaning unlike spring metals, it is perfectly happy to stay where it’s put once bent. So, the jacketing is used to offset the copper’s desire to stay put.
Coil cords have jacketing on the individual inner conductors and then an outer jacketing that covers all of those the inner conductors together. Polyvinyl chloride (PVC), polypropylene (PP), and polyethylene (PE) are all good options for inner jacketing material. While PP and PE are a little more expensive, they allow conductors more movement which enhances the cord’s retractability. For coil cords that require high retracting performance, the jacketing on the inner conductors can be polyurethane (PU), thermoplastic rubber (TPR), or thermoplastic elastomer (TPE).
The outer jacket of a coil cord is a little more important since it is the first line of defense from environmental hazards and adds the most to the coil cord’s ability to extend/retract over many cycles. Materials commonly used by coil cable manufacturers include high-elastic PVC, PU, TPR, and (TPE). Each of these has strengths and weaknesses that should be evaluated carefully for the best performance.
Conclusion
A reputable coil cable manufacturer is an indispensable resource when choosing materials for your custom coil cable solution. Make sure you communicate all the requirements for the cable as well as any time or budgetary constraints. The design team should be able to make recommendations for materials that meet your needs while taking advantage of the unique properties of coil cords.
When you’re ready to discuss your next custom coil cord project, contact the team at Meridian Cable Assemblies. We look forward to hearing from you.