Customized cable produced by a manufacturer specializing in prototyping and design can set your product apart.
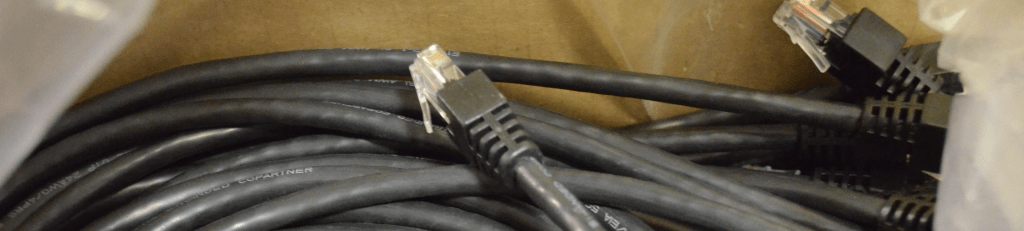
Custom Cables for Prototyping
When looking for high quality, fairly priced materials for creating a prototype, it can be a challenge to find the right wiring components for your specific product and industry. There is no shortage of options when it comes to custom wiring and it can be a challenge to determine which material will be best for your product and wiring needs. By partnering with a manufacturer on Custom Cables for Prototyping, you and your team will have a knowledgeable resource to turn to when making these decisions. This can be the difference between a successful prototype and one that does not live up to expectations.
Simplifying the Production Process
Consulting with a manufacturer capable of extruding small amounts of specialized wiring to enhance and perfect a product is an important step in the manufacturing process. There are so many choices to be made regarding wiring systems that opting not to work with an engineer, instead of making assumptions about the best type of wiring to use, can be dangerous. To determine a product’s voltage, required wire gauge, and optimal heat rating engineers work with a series of calculations to ensure that they are producing a safe and effective product. If these calculations are not performed correctly or are overlooked, the resulting product could overheat, cause shorts, fires, or even injury.
Reducing Costs by Partnering with a Cable Manufacturer to Produce Custom Cables for Prototyping
Cost is often seen as a barrier to working with a cable manufacturer. However, by working with an experienced cable manufacturing company, you can reduce the costs that are typically spent on experimenting with various products and wiring systems in an effort to determine which one will be most effective. Your manufacturer’s expertise and industry knowledge will guide you and your team to the systems that will be ideal for your product and its various functions. This will save time and the intensive research process that usually goes with choosing wiring materials without the guidance of an engineer.
Custom Cables for Prototyping Your Project
By utilizing custom materials, your product is likely to be streamlined and optimized for speedy manufacturing and assembly. This is beneficial if you intend to manufacture your product on a large scale, as much of the planning and manufacturing optimization will have been worked out previously. With a functional prototype of your project, you will be able to assess and make any modifications before it is produced on a large scale. This will cut costs while providing you with a highly customized wiring system designed for your specific product needs.
Testing Your Wire Harness or Cable Assembly
Product testing is another important part of the manufacturing process, assuring that everything works as planned and is durable enough to withstand the product’s intended conditions. Manufacturers utilize a variety of testing methods to assess quality including: advanced life testing labs, pull testing, and measuring the consistency of the product’s voltage. Understanding areas that could be improved on are important to a product’s functionality and acceptance in the marketplace. Product testing is an invaluable step in. ensuring that your product works as planned and does not need further adjustments or alterations before being manufactured on a large scale.
Working with a manufacturer is an important step in designing and producing custom wiring for a new product. By working with a manufacturer, you have the ability to create unique wires and cables that are optimized to work seamlessly with your product. Don’t hesitate to reach out to the Meridian Team to learn more about the options that exist for your next wiring project.