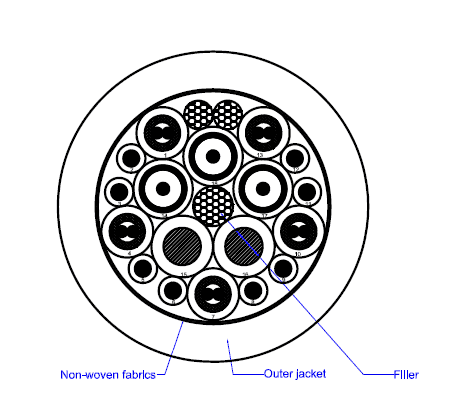
Coil cords, curly cords, coiled cords – all of these monikers refer to the same versatile product of wound cable, perfect for space-saving and decluttering a given application. Coil cords are also exceedingly durable, as well as obviously flexible, able to withstand thousands of extensions and retractions. But getting from initial concept to finished product takes many design steps in between. Arguably the most crucial of which are the different tests each coiled cord undergoes in order to ensure functionality, safety, and performance in line with the parameters supplied by our client.
Today’s Livewire News spotlight has its sights on the best ways to test coiled cord designs in order to produce the one-of-a-kind coil cables that live up to Meridian’s standards.
Starting Out with Simulated Design Testing
When our clients first meet with Meridian’s design staff, we start with covering the needs of the project, where the product will be employed, a timetable, and budget. With these factors, our team can begin to map out the process, tools, and equipment needed to complete the curly cord within the given set of parameters.
Utilizing advanced computer-aided design (CAD) software systems, our engineers can begin building out a curly cord from the very first strand of wire. Designing in this virtual space allows our team the chance to see how different iterations come together and then how these work within given simulations.
These simulations give us an opportunity to tweak certain aspects of the design in order to better meet the design requirements of the project. Perhaps a client needs a coil cord that cannot be cut where we may need to employ advanced materials in the jacketing or insulation such as Kevlar® or Teflon®. Starting with UL-listed components lets our engineers have an established point of origin i.e. a product with known specifications. Rather than trying to produce a given component from scratch, utilizing UL components means we already know the limitations and performance levels that can be expected. This provides a much better simulation and makes moving into prototyping all the easier.
Prototyping Within the Coiled Cord Testing Process
Once our team has a design in mind, the most effective strategy for overall product quality is to proceed through a prototyping phase. Prototyping allows us the chance to see how the components come together and function in the real world. It’s not uncommon for our engineers to test two or three different versions of the same product to see which combination works best for our clients’ needs. During one complex curly cord design project for a medical technology application, our team produced 14 different prototypes to find the perfect set of materials, sourcing, and logistics plans in order to meet the unique specifications of the project.
Logistics and sourcing are important variables for consideration during the prototyping stage. True, while materials play a huge role in how the product will function, almost every project undertaken has a definitive schedule that needs to be met. Seeing how the different versions come together from start to finish gives our project managers the best view possible of how a given production run will go.
Once prototyping is complete and we’ve moved onto volume production, the units are still destined for a load of different tests before they’re ever ready to be delivered to the client.
Testing Curly Cords with Automated Units
Utilizing automated testing machines like the venerable Cirris® testing units allows for testing coil cord assemblies and harnesses en masse and to exacting levels of detail. Cirris units are able to test for continuity, which simply means that the flow of data, signal, or power through the coiled cable is not impeded in any way.
Another testing parameter the Cirris units can undertake is called insulation breakdown testing. This testing regimen involves putting an excess of voltage through a coiled cable to see where insulation breaks down and can actually begin to conduct electricity. Knowing this threshold allows for incorporating insulating materials that can withstand the pressures of the application and the environment.
Using several different versions of testing protocols with our Cirris units is one of the many ways our engineers can ascertain the level of quality in each and every product we manufacture.
Meridian’s Very Own Advanced Life Testing Lab
One of the most exciting places to find yourself within Meridian’s manufacturing facilities is our Advanced Life Testing Lab. Within this dedicated space, men and women subject coiled cords to fire and ice, caustic chemicals, water, and more. All of these environmental factors are variables that require careful design in order to effectively mitigate against them. Producing a coiled cable for an automotive application, such as those seen on the backs of a semi-tractor trailer’s cab, requires a cable to withstand rain, snow, UV damage, and even chemicals like oil.
Our Advanced Life Testing Lab was created with the single purpose of testing to see how cable assemblies and wire harnesses will hold up under extreme environmental factors so that they can be counted on to perform exactly as they are intended wherever they are implemented. Seeing how different components like the insulation, jacket, or connectors perform allows a studied performance review and an opportunity to tweak the design as needed.
Different Tests to Perform with Coil Cables
With coiled cords expected to extend and retract many times throughout their useful life, these special cables are put through a battery of physical tests that see how long they can hold up. Measurements of failure thresholds and levels of compliance to specifications affords yet another opportunity for ensuring quality throughout the process. This attention to detail in quality is needed to adhere to the strict standards of ISO 9001:2015 certification, which we’re proud to maintain.
Some of the many curly cord tests that our team can perform to see where a given design rates include:
Cycles to Failure
The number of cycles that a product can achieve before fatigue and/or failure occurs. Generally this test is used with a new curly cord to decide where the threshold is. Starting out, the coiled cord is hooked up to a testing machine where length, speed, and the time spent retracted and extended are input. These all depend on the cord’s intended environment.
Once these variables are plugged into the testing machine, the unit being tested goes until it gives out. In some cases, a coiled cord may need to last 500,000 extension and retraction cycles. If this product doesn’t meet this during a cycles to failure test, our designers will continue to work at solving the limited factors.
Retraction Compliance
After a curly cord is extended, it is expected to go back to its original length. When you have a curly cord that isn’t performing well, you can see a degradation of as much as 50% of the initial retracted length. A coiled cable that has been designed well and is performing at its best should be at 95% or more. Measuring the retraction length at rest and cycling the cord through many different times allows our engineers the opportunity to measure just how well the cord’s retraction is holding up. These specialized cables need to be known that they can be counted on to keep performing their function for however long their useful life is dictated.
Cable Flexing to Failure
Curly cords undergoing this test will see just how far the cable can be strained before continuity is broken. A cable flex testing machine will test the unit based on provided variables affecting radius, rotation angle, and cycle speed. Once a cable begins exhibiting signs of mechanical fatigue and/or failure, our engineers then have a threshold to work from.
There are also several different types of fatigue that our engineers watch for during testing.
- Mechanical fatigue testing provides an excellent view of the value to which the stress/strain can be before a curly cord either fails completely or begins to show signs of failure.
- Creep fatigue measures how many cycles can be performed under high temperature testing.
- Thermo-mechanical is a combination of temperature extremes and straining within the coiled cable.
- Corrosion sets in with caustic chemicals and particularly harsh environments.
- Fretting can occur where friction is produced from sliding.
Knowing how components react towards a myriad of different variables and performing tests like these aid our engineers in producing the perfect custom curly cord to perform within the client’s unique set of circumstances.
Starting Your Own Coiled Cable Design Project
Testing in coiled cords takes an engineer and design team knowing their product literally inside and out. Meridian’s engineers are gifted men and women with years of designing cables from the very first strand of wire onto some of the most sophisticated cable assemblies in the world.
When you’re ready to start your own custom curly cord design project, trust our experienced team to ensure your product lives up to parameters needed to get the job done right. Contact us now to get started.